
近年、様々な業界で活用されているOEM。コンビニやスーパーに並んでいるプライベートブランド商品がその代表例ですが、OEMが広く普及するようになった背景にはどのような理由があるのでしょうか。
OEMの仕組みや使用するメリットを知っておけば、自社の事業に活かすことも可能かもしれません。この記事では、OEMの仕組みや製品開発の流れ、メリット・デメリット、活用事例などをご紹介いたします。
目次
OEMとは
OEMとは、「original equipment manufacturing」または「original equipment manufacturer」の略であり、「相手先商標による製造」もしくは「相手先商標製造業者」という意味の言葉です。つまり、委託企業のブランドや商標で販売される製品を、受託企業が品質管理などを行って製造することを指します。
大きなブランド力や販売力を持った企業が、高い製造技術のある企業に自社製品の製造を依頼する下請生産の一形態です。
OEMは、1950年代にアメリカのコンピューター関連企業であるIBMによって生み出されました。当初はコンピューターや電子部品の製造をメインに使用されてきましたが、現在では家電製品や食料品、衣料品、雑貨など、多様な業界で取り入れられています。
日本でも、大手コンビニチェーンがOEMを利用したプライベートブランド商品を展開したり、自動車メーカーが自社の製造ラインにない他社製自動車に自社ブランドを付けて販売したりする例があります。
OEMとODMとの違いとは
ODMとは、「Original design manufacturing」または「Original design manufacturer」の略語であり、製品を製造するだけでなく、製品の企画や設計、開発も含めてトータルに受託企業が請け負うOEMの一形態です。
中には、マーケティングや物流、販売といった製造以外の分野も一貫して提供している企業もあります。特に、パソコン業界や携帯電話業界で広く取り入れられている手法です。
OEMは、コンビニや自動車の例からもわかる通り、委託企業は自社でも製品の製造を行っており、受託企業と同等の製造力を持っているケースが多くなっています。
一方、ODMの場合、委託企業はあまり製造力を持っていないことがほとんどです。例えば、これまで販売のみを行ってきた量販店が、自社ブランドの家電を製造するケースなどが当てはまります。
OEMの3つの目的
OEMによって製品を開発する目的は、企業の業態や販売戦略によって様々です。ここでは、市場において新製品が販売され衰退するまでの各時期に合わせてOEMの利用目的を説明します。
導入期|リスクの低減とコストダウン
新製品が初めて市場に登場する導入期は、市場規模がまだ小さく、製品の将来性や発展性が不確実です。そのような状況で製品の製造ラインを新設することは、多大なコストがかかるだけでなく経営リスクをともないます。
OEMで製品を開発すれば、自社で新たに製造ラインを開設する必要はありません。そのため、コストやリスクの低減を図りながら新製品を市場に出し、その将来性を見極めることができるのです。
成長期|製品開発にかかる時間の節約
新製品が軌道に乗って市場規模が拡大し始めると、次は製造ラインの拡充・多様化のニーズが発生します。とはいえ、自社にとって手薄なラインをまた一から開発するとなると時間がかかってしまい、市場の成長スピードに追い付いていけません。
すでに安定した製造ラインを持っている企業に製造を委託すれば、開発にかかる時間を節約できます。
成熟期|製造ラインの確保
製品の需要がひと段落する成熟期に入ると、拡充した製造ラインの中でも採算の取れないラインから撤退するという選択肢が発生します。
とはいえ、販売店や顧客との利害関係もあり、採算が取れないからといって簡単に撤退できるとは限りません。そのような場合には、製品供給の確保を目的としてOEMが採用されます。
このように、市場規模や生産規模の変動に合わせて戦略的にOEMが使い分けられています。
OEMの事業の流れ
製品の種類や業態によって異なりますが、OEMによる製品開発は以下のような流れで行われます。
1.企画の提案
委託企業のマーケティング方針や顧客ニーズ、課題を元に製品の企画を進めます。受託企業は、ターゲットや予算、納期、販売計画などをヒアリングの上、具体案を練って開発をスタートさせます。
場合によっては、受託企業から企画を持ちかけることもあります。自社の持つ技術や製造ラインでパッケージングを固め、委託企業のブランドを付けて販売することを提案します。
2.サンプルの試作、チェック
企画にしたがって、受託会社がサンプル品を制作します。品質を細かくチェックし、改良すべき点があれば、さらに試作を重ねていきます。納得のいくサンプルができあがるまで、何度も改良を繰り返すこともあります。
3.契約締結と発注
試作によって製法や材料、内容量、パッケージなど、製品の細かな仕様が全て決定したら、受託企業が見積もりを作成します。双方が合意すれば契約締結へ進み、本格的な製造に入ります。
4.生産体制の確立
製造の本格始動にあたり、受託企業は試作から量産体制へ移行するよう、確認や調整を行います。必要な資材の確保や調達ルートの確定、製造を担当する工場との打ち合わせ、製造期間や納期の確認など、委託企業の要望通りに生産を進められるよう環境を整えます。
5.製造開始
量産体制への移行が完了したら、OEM商品の製造を開始します。
受託企業と工場は、仕様通りの製品に仕上がるよう品質チェックや評価を行い、生産ラインの管理を行います。
また、納期も厳重に管理し、生産スケジュールに遅れが出ないようコントロールします。日々の品質チェックや進捗管理で得られた情報は、委託企業に共有するようにします。
6.製品の改良やリニューアル提案
製品が市場に出回ると、消費者からの反響や評価が調査され、製品の改良が検討されます。市場の反応が大きければ、リニューアル版が企画されたり、第2弾、第3弾と新商品が開発されたりすることもあります。
OEMの4つのメリット
OEMでの委託製造が多様な業種へ広がりを見せる背景には、どのような理由があるのでしょうか。OEMを利用する4つのメリットを紹介いたします。
コスト削減効果
最も代表的なメリットといえるのが、新製品の製造におけるコストカットです。
製品を新たに開発して大量生産の体制を作るにあたり、大きな負担となるのが設備投資と人件費です。
資材の調達ルートを一から確保し、機材を購入して製造方法を確立、その方法をマニュアル化して人材を育成するためには多大な資金と労力が必要になります。
すでに量産体制が確立された製造ラインや技術力のある人員を持っている企業にOEMを委託すれば、これらのコストを削減して製品開発にあたることができます。
市場変化への迅速な対応
前述の通り、自社で製造ラインを新設するには多大な資金と労力、そして時間が必要です。市場のニーズを受けて新製品製造に乗り出したものの、完成する頃には需要のピークを過ぎてしまったという事態も起こりかねません。
市場のスピード感についていけないと、せっかくの投資が無駄になってしまいます。
OEMを利用すれば製造までにかかる時間を大きく削減できるため、よりスピーディに製品を市場に流通させることが可能です。市場ニーズの変化により迅速に対応し、機会損失を回避することができます。
経営リスクの低減
近年では、新製品開発の初期段階でOEMを使用し、利益が確実になってから自社製造に移行するというケースも増えています。市場ニーズをとらえた製品を迅速に世に出し、反響によって量産に入るかどうか決定したほうが、経営リスクを低減できるためです。
コア事業への選択と集中
OEMを用いてコストカットやリスクヘッジをはかることは、経営資源の有効活用にもつながります。
限られた予算や人員を確実性の低い新規事業に大きく投入することは、企業にとってリスクをともないます。自社の強みをより強化して市場の変化に応えるためには、弱みを切り捨てることも必要です。手薄な製造ラインを外注してしまうことで、コア事業に注力することが可能になります。
OEMの2つデメリット
多くのメリットがあるOEMですが、デメリットがあることも把握するべきです。OEMを利用する際には、デメリットにも留意して検討を進めるようにしましょう。
社内ノウハウの不足
OEMで製品開発を行う代表的な弊害として、委託企業に製造ノウハウや技術が蓄積されないという点が挙げられます。
受託企業から製造に関する情報は共有されるものの、日頃蓄積する経験は委託企業には蓄積されにくくなってしまいます。
また、社内に製造知識や経験のある社員が不足してしまうため、その製品についてクレームや修理の依頼があったときに、社内対応が難しいという問題も発生しやすくなるでしょう。
責任の所在
製品について重大な欠陥や不良が判明した時に、委託企業と受託企業のどちらが対応するのか、責任の所在があいまいになってしまうというのもよくあるトラブルです。
一般的には、トラブル発生時の対応は契約書面で定められていることがほとんどです。しかし、受託企業に加えて実際に製造を担当した工場や資材の調達先など、関係企業が多くなるほど原因の究明も困難になります。責任を押し付け合う事態にならないよう、役割分担を明確にし、日頃からの情報共有を徹底するよう努めましょう。
企業のOEMの事例
国内でOEMによって製品開発が行なわれた実際の企業例を2つ紹介します。
小林製薬のスピーディな新商品開発
医薬品や日用品の製造を行う小林製薬は、積極的にOEMを活用している企業として有名です。国内向け製品におけるOEM取引社数は、約100社にものぼるといいます。その理由は、小林製薬が開発スピードの速さに重点を置いていることです。
同社では、全従業員から製品アイディアを受け付ける提案制度を設けており、早いものだと提案から13ヶ月で新製品を市場にデビューさせているそうです。新製品をスピーディに商品化することで、次々と新しい市場を開拓し、そこでトップシェアを獲得することに成功しています。
トヨタの軽自動車参入
国内最大手である自動車メーカーのトヨタは、2011年に同社初となる軽自動車「ピクシス スペース」を販売。これは系列会社であるダイハツの「ムーヴコンテ」をベースに、OEMで製造された車種です。
自動車の販売台数が落ち込む中で唯一成長可能性があるのが軽自動車であったことから、トヨタは生産ラインを新設せずに、OEMを利用して参入しました。
この背景には、自動車は量産効果が大きいという理由があります。同じく軽自動車をOEM提供しているスズキの鈴木会長は「1車種を12万台生産するか、6万台生産するかで1台当たりのコストが3割も違う」と述べています。受託企業にとってもOEMのメリットは大きいことがわかります。
OEMを検討する際の注意点
最後に、OEMによる委託契約を結ぶ際の注意点を解説します。
技術の流出
OEMに参入する場合、製品の品質を確保するために委託企業が受託企業に技術支援を行うことがあります。受託企業がその技術を勝手に流用することはもちろん契約で禁止されますが、技術の一部をアレンジして製品を作られてしまう可能性も。
受託企業が競合企業になってしまわないよう、技術の取り扱いについて明確に取り決めることが必要です。
製品の横流し
製造したOEM製品に他社のブランドを付けて販売するという、横流しのリスクも考えられます。もちろん、製品の製造方法や仕様書は委託企業の財産ですので、横流しは許されません。契約書を作成する際は、所有権や知的財産権は全て委託企業に帰属することを明記しましょう。
責任の所在
OEMでは委託先業と受託企業、実際の製造を担当する工場など、複数の企業が関係していきます。製品に不備があり、消費者が不利益を被った場合に、どこが責任を負うのかも明確にすべきです。契約書では、受託企業や生産工場に過失が認められる場合には補償を求める旨を盛り込むようにしてください。
OEMの仕組みを自社のビジネスに活用しよう
OEMは、生産コストや参入リスクを大幅に低減しながらスピーディに量産体制を確立できるなど、委託企業にとって多くのメリットがある製品開発手法です。その多くの利点から、今では電気機器業界に留まらず、様々な業界の企業で取り入れられています。
最近では受託企業がOEMサービスをパッケージ化していることも多く、新規参入の障壁も低くなっています。契約における注意点に留意しながら、自社での活用を検討してみてはいかがでしょうか。

あなたにおすすめのお役立ち資料を無料ダウンロード
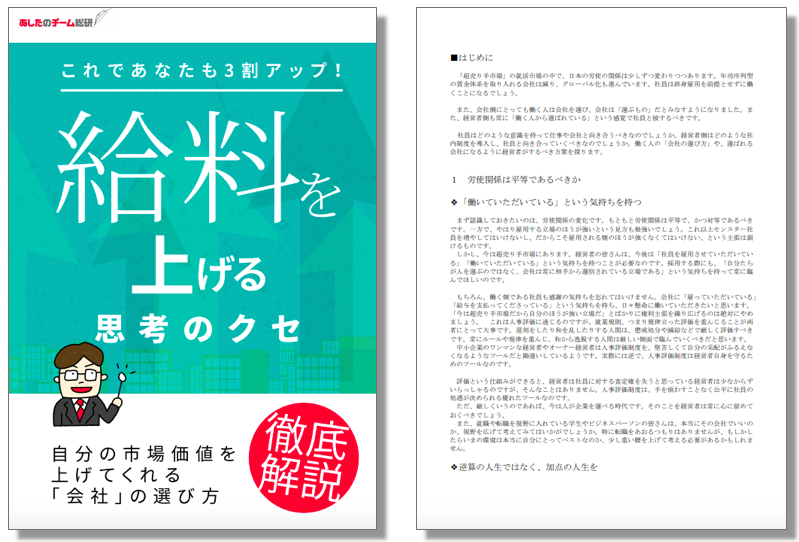
ダウンロードは下記フォームに記入の上、送信をお願いいたします。
【無料ebookプレゼント】これであなたも3割アップ!給料を上げる思考のクセ
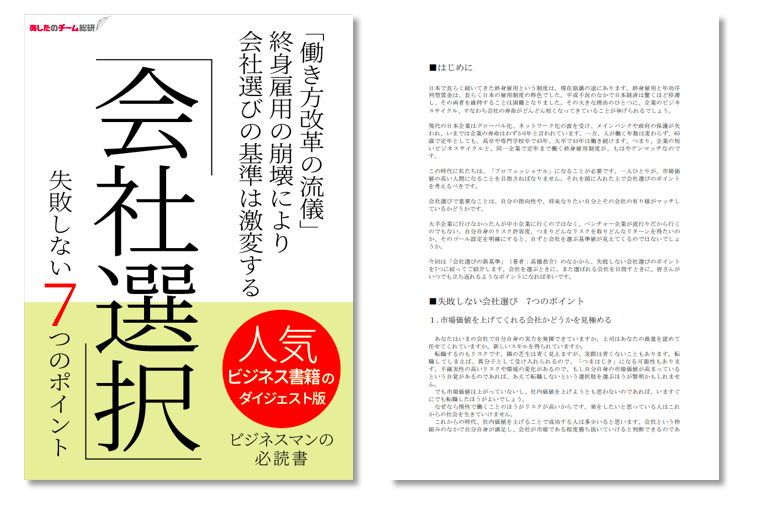
ダウンロードは下記フォームに記入の上、送信をお願いいたします。
【無料eBookプレゼント】失敗しない会社選び7つのポイント
あしたのチームのサービス
導入企業4,000社の実績と12年間の運用ノウハウを活かし、他社には真似のできないあらゆる業種の人事評価制度運用における課題にお応えします。

ダウンロードは下記フォームに記入の上、送信をお願いいたします。
サービスガイド

ダウンロードは下記フォームに記入の上、送信をお願いいたします。
あした式人事評価シート